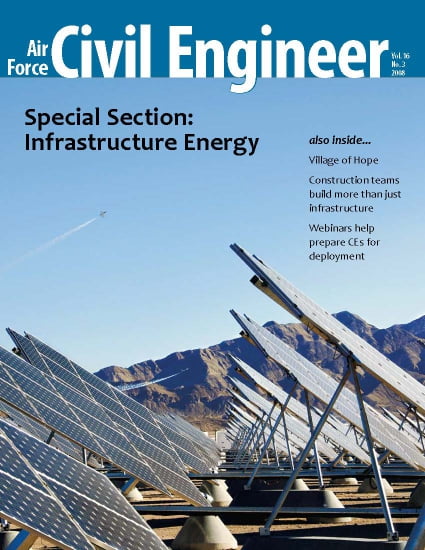
The Infrared Heating Advantage
Industry Publication
The Air Force Infrastructure Energy Strategic Plan requires the Air Force to use less energy as well as use energy more efficiently. Infrared heat may be the most effective method of heating large-volume industrial spaces such as warehouses, maintenance bays, and hangars. These facilities typically have a
high energy footprint (BTU/sq Ft) due to large infiltration loads, vehicle access requirements, poor insulation, and high ceilings. Here, forced-air heating systems are neither efficient nor effective at providing a uniform 55°F wintertime work environment for occupants.
How IR Works
About 53% of the solar energy striking the earth is in the IR spectrum, which is just above visible light (wavelength > 0.7 μm). This is the energy that heats the inside of your car even though the outside temperature may be cool. The sun heats the car which, in turn, transfers heat to the air inside. Infrared heating systems work in a similar manner.
The typical IR heating system consists of a burner, a combustion tube, zone thermostats, and a controller (below). Reflectors may be added for directional heating and to protect potentially flammable surfaces, such as wooden roofs. Thermostatic feedback through the controller maintains set-point temperature within the facility.
In contrast, to satisfy heating demand, forced air systems heat the air, pump it into a space, and rely on the energy-intensive process of convective air-to-object heat transfer. IR heat bypasses the air transfer medium, thereby improving heat transfer efficiency. Because large air handlers, pumps, water control loops, and heat exchangers are eliminated, IR heating systems are desirable from a maintenance perspective as well.
IR heat is directional, with reflectors focusing energy toward a target area. When properly installed, IR heating eliminates cold spots in large-volume facilities. Because infrared heat warms like the sun, occupants feel more comfortable at lower set-point temperatures. Since IR systems do not heat air directly, they are not subject to air stratification. They are also less affected by open doors and high infiltration or air exchange rates.
Actual Performance
Little Rock AFB, Ark., demonstrated the effectiveness of IR heat systems by installing them in three large volume facilities, including Bldg 250, a 152,000-square foot jumbo hangar. After the retrofit, the average MBTUs of natural gas used for winter heating dropped from 21,080 to 11,240, a 44% reduction when corrected for weather effects. Based on FY05 natural gas rates ($7.63 per MBTU), this project was estimated to provide the base an attractive 7.8 year payback. With FY07 rates at $9.80 per MBTU, the payback is now down to about 6 years.
IR heat has the potential to significantly reduce the high energy footprint of large Air Force industrial facilities and help meet Executive Order 13423 energy goals. It is recommended that all installations with conventional heating in large volume industrial facilities consider IR heat retrofits as replacements.
Mr. Adams, a support contractor at the Air Force Facility Energy Center, HQ AFCESA, Tyndall AFB, Fla.,is a professional engineer. 1Lt Miller was formerly the Chief, Maintenance Engineering, 314th CES, Little Rock AFB, Ark.; he is currently the squadron’s Readiness and Emergency Management Flight Chief.
Adams, T. A. (2008). The Infrared Heating Advantage. In AirForce Civil Engineer Magazine (3rd ed., Vol. 16, p. 22). Tyndall AFB, Florida: Professional Communications staff at the Air Force Civil Engineer Support Agency.
Adams, T. A., P.E. HQ AFCESACEN 1 Lt, & Miller, R. C., 314 CES/CEX. (2008). The Infrared Heating Advantage. Air Force Civil Engineer, 16(3), 22.
#large facilities, #aircraft hangar, #smaller footprint, #less energy, #more efficency